Modifications to the XPAG Water Pump
Text and slides presented by Eric Worpe at the T Register Rebuild event, April 2023
These are the slides and additional text used by Eric Worpe at the T Register’s Rebuild event held at the British Motor Museum, Gaydon in April 2023. Eric used hand drawn flip chart diagrams.
You can click/tap on each slide for a larger picture.
1. Early Water Pump Schematic
This is a schematic of an early type of pump using a pin driven floating graphite cup thrust against a fixed graphite block secured in the pump housing. The floating cup is spring loaded through a dished washer and a rubber washer which seals off the cup from the drive spindle. The rubber washer is not shown on the diagram.
The graphite seal is long lasting but the rubber washer hardens and allows coolant to leak past the spindle into the drainage chamber. Coolant should then escape through the drainage hole but can also enter the adjacent ball bearing.
To limit leakage into the ball bearing, a secondary seal comprising a felt washer between two steel washers is keyed to the spindle. The outer periphery of the felt washer rubs against the wall of the drainage chamber but soon looses its effectiveness in sealing against leakage into the ball bearing.
This type of pump’s life is determined by the rubber washer which it seems is no longer available.
2. Later Water Pump Schematic
The schematic shows the later pump with a spring loaded rubber bellows type graphite seal and a phosphor bronze thrust washer fused to the impeller. The bellows has a tapered outer section which makes for an effective seal in the pump’s housing.
A similar secondary seal as in the early pump is again used, with the felt and steel washers clamped between the circlip and inner race of the ball bearing. The shoulder of the spindle is an integral part and serves to locate the spindle relative to the ball bearing. The bronze thrust washer is polished to reduce wear of the carbon block.
This type of pump is the most suitable for rebuilding.
3. Modern version of Water Pump
This slide hows the modern version, which seems to have been made to a price rather than quality. It uses a press fit cartridge with a spring loaded graphite seal thrust against the cast iron face of the impeller. The shoulder on the spindle has been replaced by just a circlip which can be displaced if the pulley nut is tightened robustly.
The secondary seal has been omitted and the drain hole reduced in size which results in it rusting closed when leakage occurs. A blocked drain hole and absence of a secondary seal limit the life of the ball bearing.
It is advised to commission the pump by running it dry. This coats the thrust face of the impeller with graphite. The graphite seal thus becomes sacrificial in laying a graphite film over the coarse grained surface of the impeller.
4. Modifications to old water pumps
The later and modern versions of the pump can be rebuilt with either a bellows type seal Ref. NB021, or a press fit cartridge seal type FB-12L.
The NB021 version will need to use the impeller with a bronze thrust face which ought to be polished, and this version may also need the housing for the bellows machined to give a clean surface. Unfortunately the NB021 has parallel sides that fit in the housing and relies on a substantial rim to effect a seal, hence the need to machine the seating.
If the seating is too badly corroded, one could bore out the pump’s body and fit a brass seat, preferably with tapered sides for the bellows.
The circlip can be replaced by a machined collar which is either plug welded to the shaft or fixed using a roll-pin. The front face of the collar should be aligned with the front face of the previous circlip as this sets up all the relative locations of bearings and seals to the impeller.
The drain hole in the pump’s housing can be opened up and a further restriction to any leaked coolant contaminating the bearings could be provided for by a pressed in sleeve located as shown in the diagram.
5. Conclusions
A simple rebuild is limited to replacing seal and bearing.
Note that the retail available seal; is NOT suitable if the pump housing’s seat is corroded.
Beneficial modifications are dependent on having access to a lathe (and MIG welder).
Sources
1. Pump Rebuild EP Services (https://www.ep-services.co.uk), Unit 1 Central Trading Estate, Cable Street, Wolverhampton, WV2 2RJ
Bore out housing to take a larger seal unit and fit ceramic thrust face to the impeller and sealed bearings. Cost £75-£85. Lifetime guarantee.
2. Racetorations Ltd (https://www.racetorations.co.uk/product/mg-tb-f-xpag-water-pump/), Gainsborough, Tel 01427 616565
Redesigned internals and 6 bladed impeller with claimed double flow rate. Includes pulley. Cost £195 + VAT. Outright purchase.
Considerations to extend bearing life
- Sealed bearings – grease is kept clean
- MGB plastic 7 bladed fan – reduced vibrations
- Toothed fan belt – allows reduced belt tension
Note that washers can be found on the internet but dimensions are rarely given.
6. Further information on the FB-12L Seal
The replacement cartridge seal type FB-12L seems to be an exact fit for the pump. It’s intended for a 33.4 mm dia. bore-hole and a 12 mm dia. shaft. The displacement from the flange seating to the impeller is 11.5 mm which also matches the original set up.
It also has a self contained ceramic thrust block for the graphite seal. For this to be effective the support sleeve for the ceramic block needs to be a tight fit on the 12 mm dia. spindle. However, the spindle area in front of the impeller is often corroded, so a sealant should be used to secure the sleeve.
I suspect that a suitably machined press mandrel may be needed to press the body into the housing and the sleeve on to the shaft at the same time. If using a sealant between the shaft and the sleeve, the impeller will need to in position before the sealant hardens.
7. Benefits of a 6 bladed water pump
Is a 6 bladed water pump worth fitting? A high coolant flow means reduced local hot spots and a more event temperature distribution throughout the engine.
Pre nodular castings are prone to cracking, so reducing thermal stresses in an engine are worth considering.
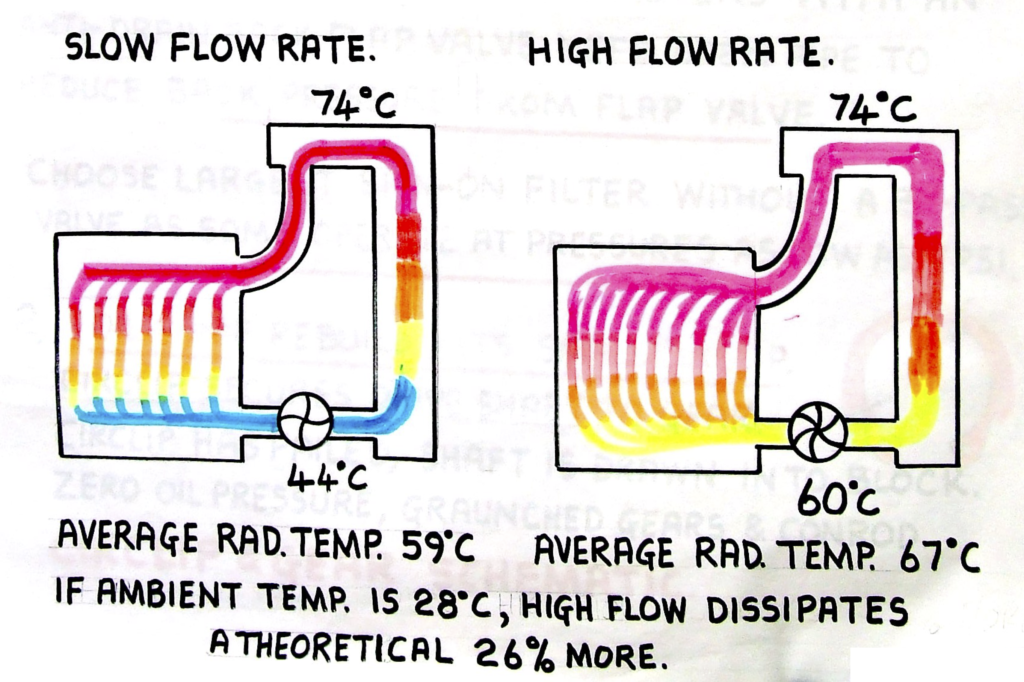
It’s uncertain whether it is worth fitting, but there is a theoretical idea based on Newton’s Law of Cooling which suggests it could.
Consider an engine running with a thermostat fully open at 74º. A low coolant flow would develop a large temperature difference. A high coolant flow would reduce the temperature difference, and also result in a higher average radiator temperature, so the engine can work harder for the same maximum coolant temperature of 74º.