Reproduction in whole or in part of any article published on this website is prohibited without written permission of The MG Car Club.
The birth of a new car, or re-hashing of an old favourite?
“Go on, Dad, tell us how you make a new car! Tell us, please!” I wish my kids would ask me this, but they now just want to drive them. I have brought home many new cars over the 29 years I have worked in the automotive industry. In the old days, they would fight to be the first to sit on the seats, crawl through ski-hatches or just play with the radio. Our drive has seen many Land Rover and MG Rover products as well as countless competitor vehicles over the years, but recently it has been MG TFs gracing the impressed fake cobbles at the front of Pogson Towers.
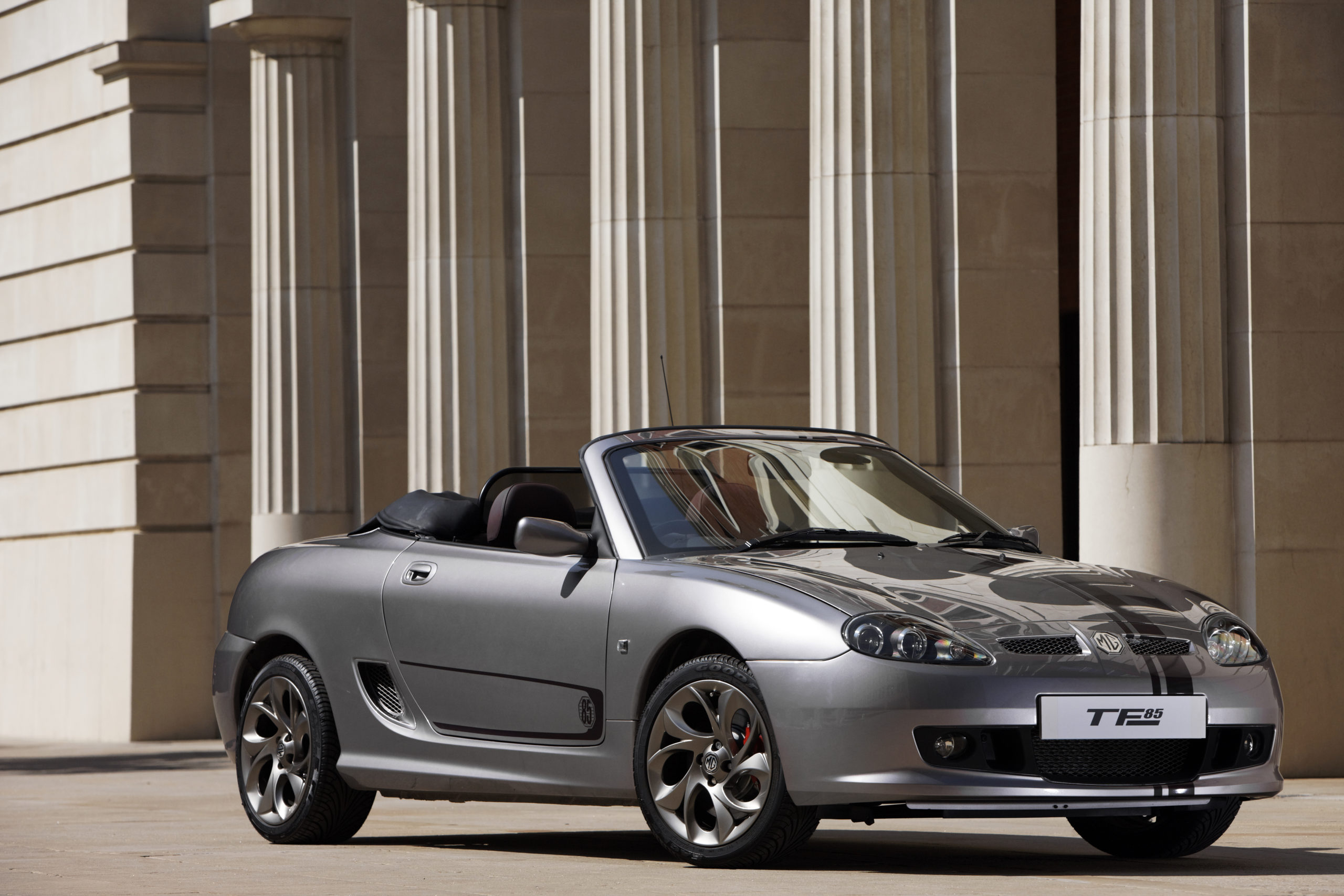
Anyway, where was I? Ah yes, dear reader. This is the point in the magazine where you gain an insight into the world of MG through an “industry insider”. I am currently on the inside, not retained at Her Majesty’s pleasure, but by those nice people in SAIC (Shanghai Automotive Industry Corporation). I work in the UK Technical Centre (SMTC), now housed in what the old ‘uns call the Sales Block at Longbridge. So I am paid to talk and worry about MGs all day. As my kids (or Clarkson) would say “How cool is that?” I must have one of the best jobs on the planet.
- I am based at Longbridge, on the edge of the beautiful Cofton Park.
- It is only 7 miles from home.
- I am surrounded by some of the best brains in the business.
- I can go and play at building cars any time of the day.
- I travel to China regularly, enjoying great people, food and tea.
- I have a management who allow me huge scope and freedom.
- Humour is encouraged.
- Every day is a challenge either culturally or technically.
- Every day is literally therefore a school day.
- I am paid well for all of the above.
By way of some personal CV highlights, I started in September 1980 as a Graduate Trainee for Land rover in Production supervision, in the days when Foremen wore red collared white coats. Along the way, I have run Competitor Analysis, Manufacturing Engineering teams, managed Technical Research for Range Rover and been the technical link between LR as manufacturer of power train and people like Morgan and TVR as customers. I have run Logistics and Laboratory functions, managed recruitment activities, been responsible for 53 pieces of material handling equipment, 40 fitters and drivers and a fleet of 60 Reliability cars. Latterly I was resident in Shanghai, teaching young, green apprentice Engineers how to design, test and build engines. I wrote a book (“Carry On Car-Making”) about my experiences if this literary babble whets your appetite.
It is however, my current job which may interest you the most, although along the way I was the Power Train Project Manager for the MG RV8 and more recently the Rover V8 Auto and MG V8 Auto (launched in Australia just before MGR’s demise). I can tell you where the Maestro part is on the RV8 engine, if I want to show off, or annoy the owner of such a car. I should know, as I specified the engine and how it was made up from various specs of unit in the LR catalogue and some old TR8 and MGB parts.
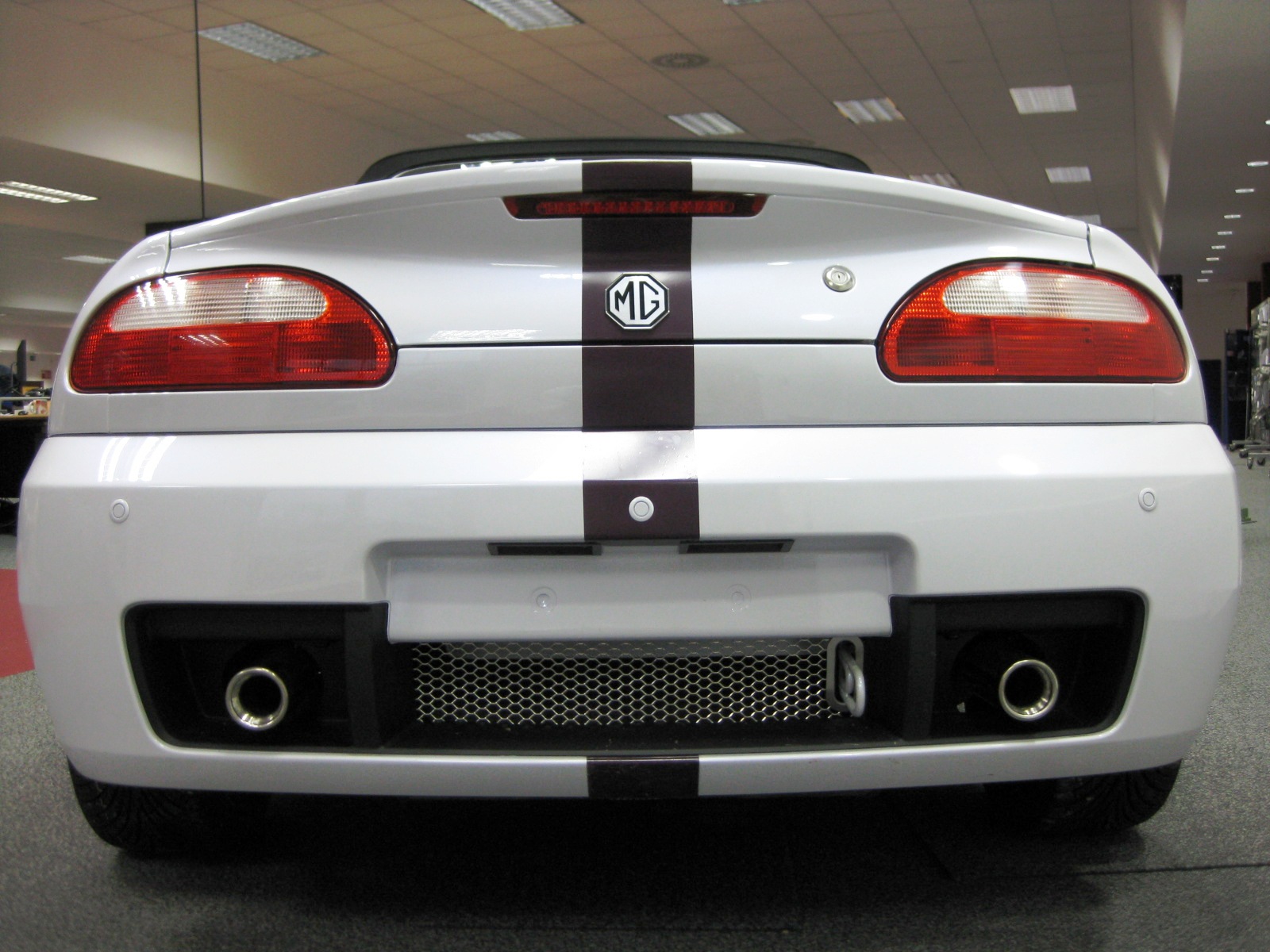
Currently I am the holder of three jobs; this being 2009 and SMTC being a caring, sharing employer:-
- I am Programme Manager for the MGTF 85th Anniversary, now in “volume” production.
- I am responsible for day-to-day Current Engineering matters on the TF.
- I am also one of the SMTC’s four Quality Engineers, supporting our colleagues in MG motor Manufacturing, but also providing input to the new product programmes coming out of SMTC in the UK and China.
All these activities stretch the brain somewhat, test patience and fore-bearing and are above all, worthwhile things to do with one’s time. In an age where the previously superior and self-important but ultimately mis-guided Finance Beings have now been somewhat discredited, I have always believed that Manufacturing is an honourable pastime. In a Production environment, we take resources, marshal them effectively and efficiently to create wealth.
Now that I have that off my chest and feel entirely self-righteous (writing this as I am, sat by the shore of Windermere whilst my lovely wife potters around the shops), we can continue with the story.
A car, or even a new part of a car, be it wheel, button or washer, has to go through a long period of planning before it is offered for sale to you. Our job as Engineers is to ensure that the washer, however humble, does not rust, fatigue or fail in its lifetime supporting the cup-holder on your new vehicle. If it did, you may spill your cup of expensive CostalottaMac coffee, scald your leg and sue us.
We take our jobs seriously, because we have to. Not just because of Product Liability issues, but because we genuinely care about cars. Many of us in SMTC are real petrol-heads; our MD has exchanged his Lotus Elise for an Exige and even the humble Engine Calibrators race and rally some extraordinary vehicles, because they are mad and love it. More horse-power, anyone?
Many of these Engineers are at the top of their tree and in many cases were the same boys and girls (we need more of these, please, if there are any parents reading) who were employed in MG Rover. In some cases they are out of their trees, as it helps to have a few “mad professor” types around for the good new ideas.
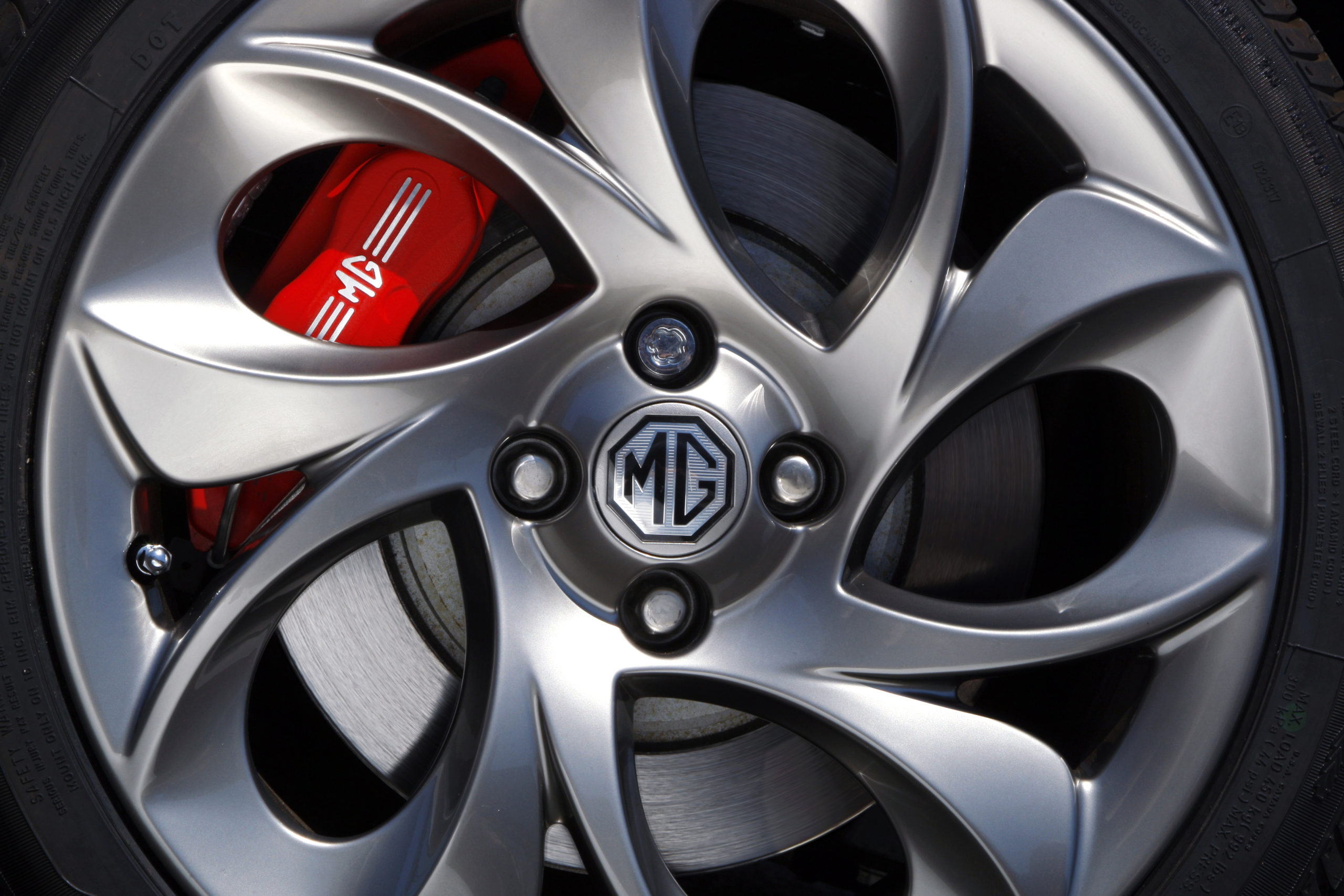
Any (motor) manufacturer the world over uses their Engineering resource in much the same way to create product. The example of MG Rover is quite a good one, as it combined all the learning from the past, including Honda (whom we should have stuck with, but Maggie had different ideas), BMW (we learned a lot from each other) and home-grown processes. We would start any new project proposal for anything from new buildings to a model-year change or new car with a proposal paper, usually penned by the Product Planning function, but in reality anyone could raise one. The proposal was refined and detail was added in the following sequence:-
- PPL (Project Proposal Letter)
- PIL (Project Investigation Letter)
- PPL (Project Policy Letter)
There was a prescribed group of functional representatives who were copied with the documents at each stage and a debating forum for each one. A time limit was set for responses, which sometimes bore a relationship to the complexity of the subject and often did not! The impetus for the subject could be legislative or commercial. It could be driven from without or within the Company.
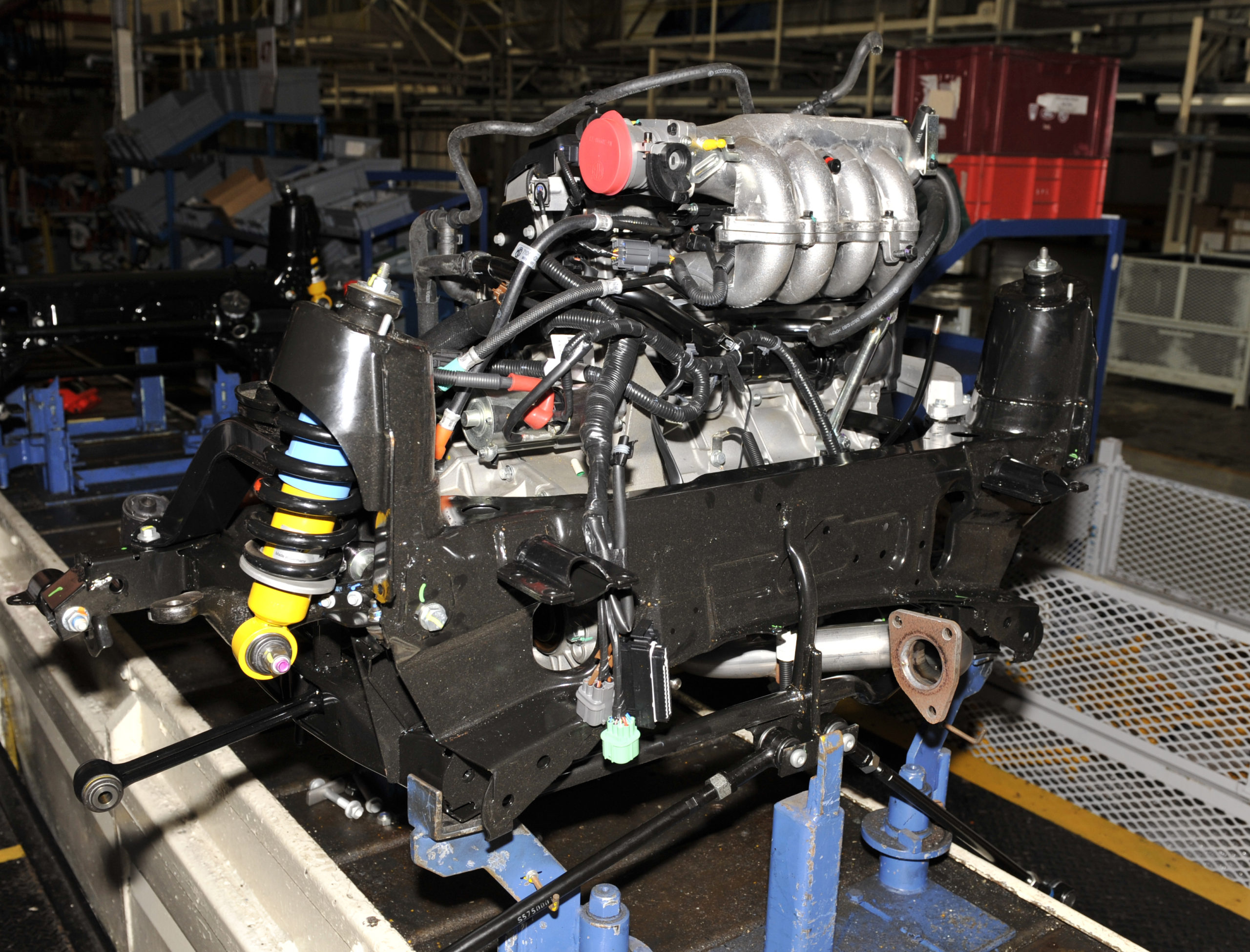
The PPL outlined the project, be it a new transmission, a new market variant or a new use for an old building. The scope was huge, but it was a process which all knew about. All functions had their “ten penn’orth” and recorded their support or otherwise. Any costs in terms of resource and facilities, D&D (Design and Development) or Capital investment were recorded. It was a good system, but was subject to some “manipulation” by unscrupulous individuals or those with a personal agenda as are any human endeavours, but it was a process.
The PIL was a second round of expressed views and fact-gathering, where we could all firm up costs and impact, once the PPL had passed through the hands of the Board and given approval to go further. The PIL as a process itself cost money to look at the PPL responses and do some more detailed work.
Once the PIL had been approved, the PPL was issued by the Board and outlined the extent of the Company’s commitment to the project and how much money would be made available.
For example, I wrote the PPL for the cessation of the “T” series engine (a real beauty, in NA or turbo form). The reason for this was that at the time we had the KV6 2.0L engine in the product portfolio, and it made no sense at our volumes to have two 2-litre engines side by side and the KV was emissions compliant for the future, whereas T was not. The real reason was that at the time, BMW wanted the space occupied by the T series cylinder block line in North Works to be replaced by the new MINI (R50) body pressing plant. This was an ambitious plan to bridge the railway and create a new face to that old part of the Longbridge plant.
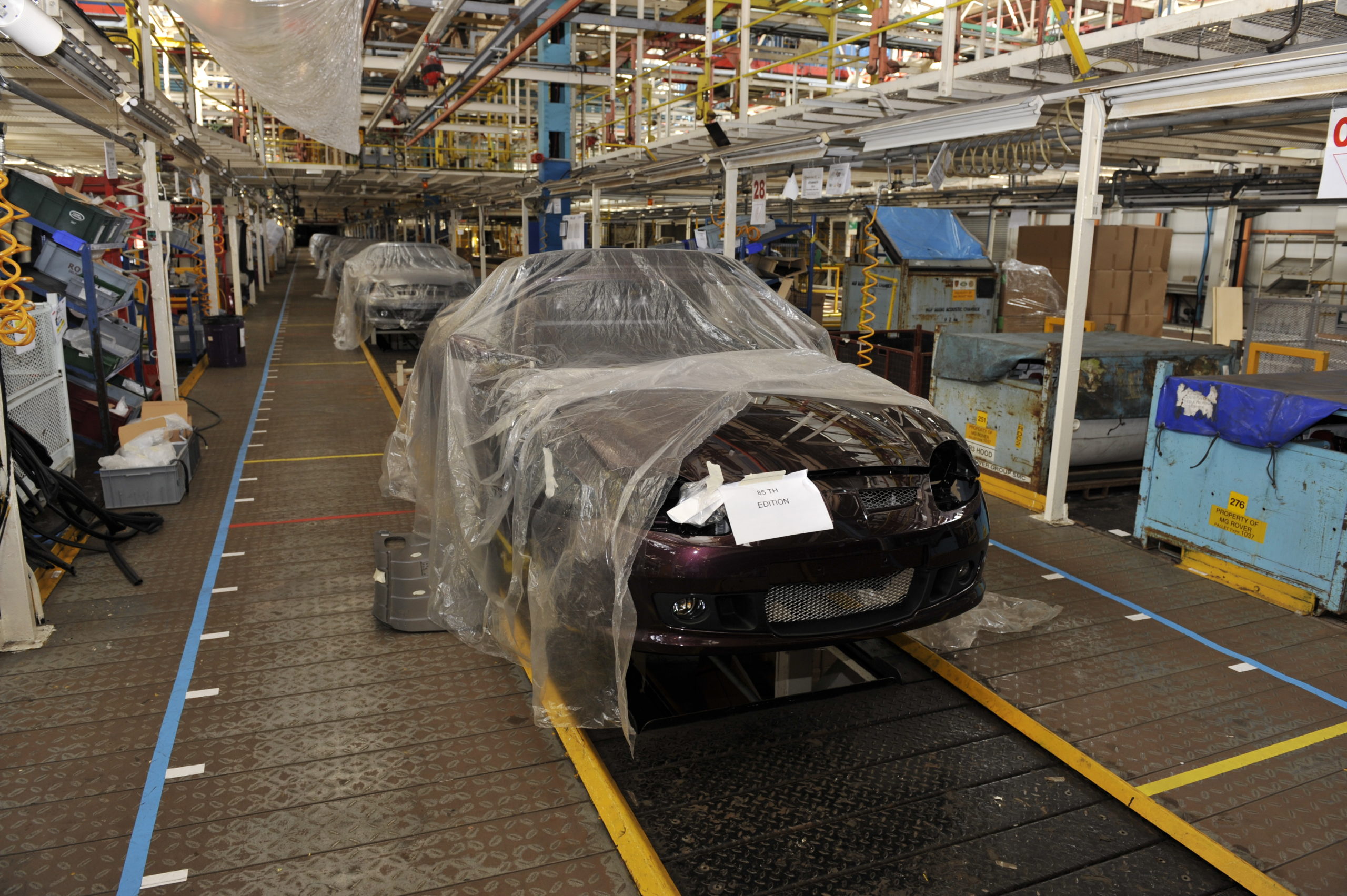
Of course it never happened, as BMW always had other plans, although after that the site was considered seriously for the location of BMW’s new NG engine factory, now at Hams Hall. What did happen was that the truncated engine line was ripped up and the building slowly lapsed into total decay.
An MG example was the PIL for an MG Auto version of the manual 260 MG ZT. This was to be sold in the only market which should ever have been pursued for the auto in my opinion, as Down Under was a big V8 consumer at the time – still is. The content to the PIL was simple and a PPL was never produced, to save time on the process. The idea was to use the MG suspension set-up and the body treatment, interior appointments for MG, but use the Rover V8 Auto power train, all parts that were known and existed, so was “just” a case of assembling the parts in a new way. Australia is a bit hot, as far as I remember and places like Alice Springs are where many auto producers go to conduct hot environment testing. We had many a debate on the temperature spread of the continent and whether we could just recommend it for use in only certain states to save money on extra test work and the need for heavy-duty cooling packs. In the end I believe we “Launched” the car for sale after testing there and then the Company folded. Tragic.
“So what happens today? How did the 85th Anniversary MGTF come about?” I hear you ask (well, those who are still awake). Within SAIC, there is a similar process, which culminates in a NOD (Notice of Decision) from the central planning function. I have the 85th NOD in my file, as it was this piece of paper that gave the authority to proceed with the project on 24 November 2008 and for me to use when three weeks later I was given the task to pick up the project and run it.
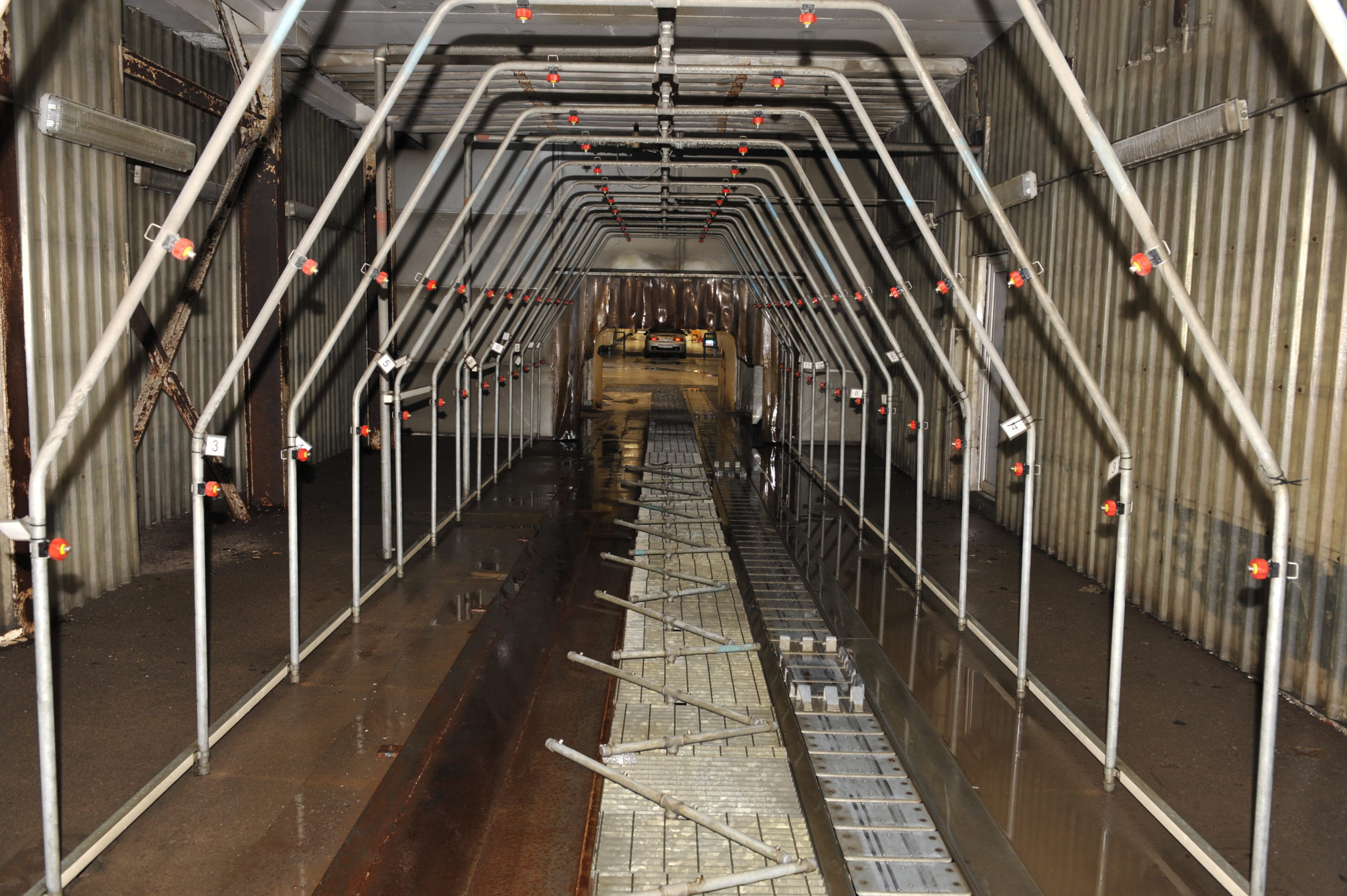
The rest as they say is history, but what you may be wondering is how come for what really amounts to a mere face-lift for the car, it was not until April that the car was seen in public and was only offered for sale in mid summer? What happens over seven months?
Any car that we develop for you, the consumer, must be fully validated. Whether we make one or one hundred thousand, the car must be fully tested and safe. Your safety is paramount. We Engineers spend much of our time researching your safety, ensuring that we meet standards and confirming that these are maintained.
The 85th features a new, more mature, more competent more damped suspension than any TF before it. Also, the steering on the 85th and now the 135 is measured to within minutes of a degree for the first time in the car’s history, to improve your driving pleasure and keep the tyres in optimum contact with the road. (If you have a car made before 2009, you can have the bump-steer checked on a “John Bean” or similar 4-wheel laser alignment rig at a reputable dealer or tyre-fitting bay). To enjoy the 85th suspension improvements you have to invest in one! There are various upgrades for the older cars such as a VHS kit, but the 85th package with wheels, dampers, bigger ant-roll-bars and links, plus the aubergine leather and decal set is the “Real Thing”.
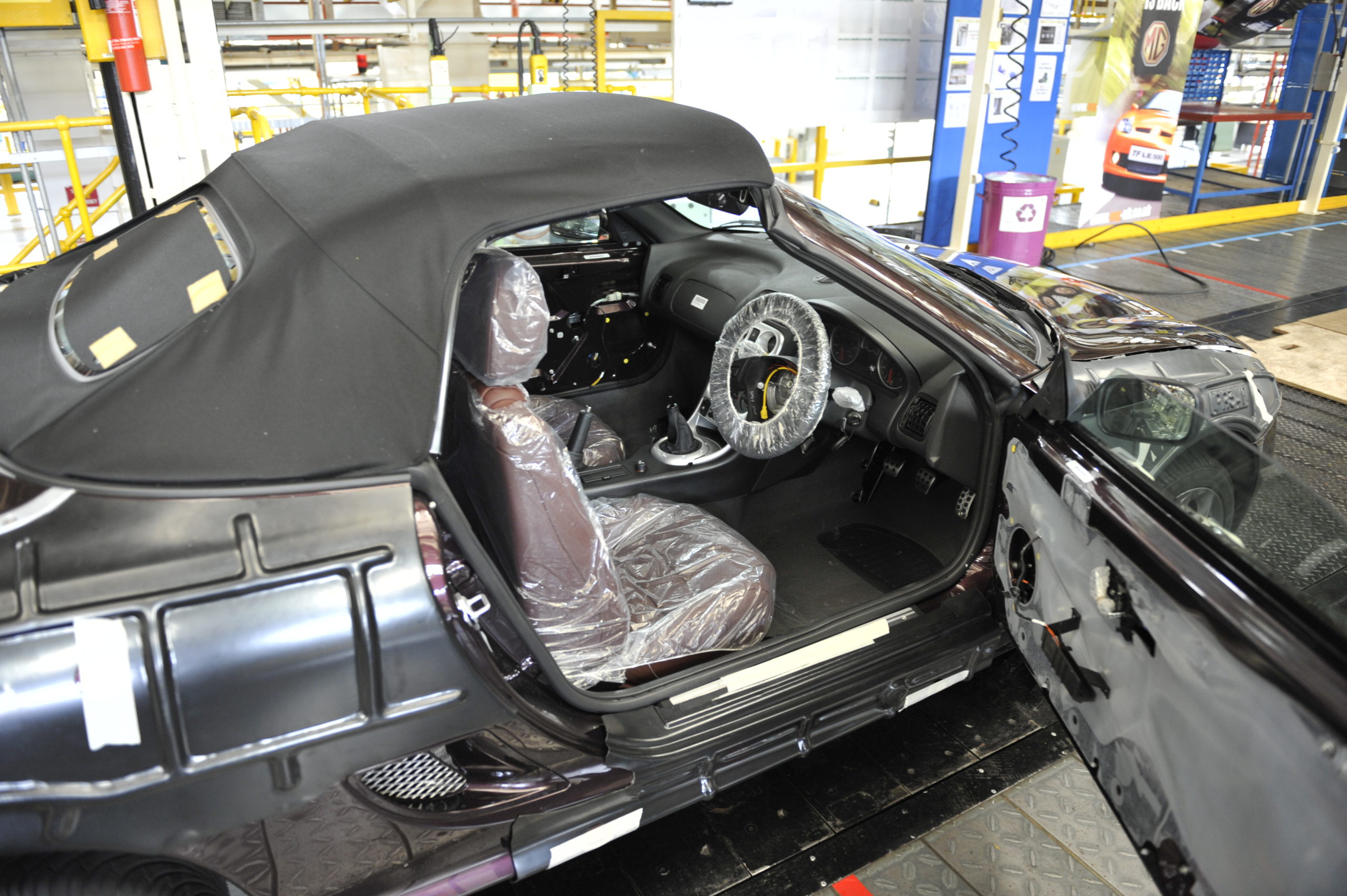
All the chassis improvements to create the 85th specification are listed below:-
- Bigger diameter Eibach ant-roll-bars (18 to 20mm rear, 20 to 25mm front)
- Rubber bushes to suit from Bull Rubber UK.
- TRW solid ball-joint ARB links to the suspension.
- Mono-tube rather than twin-tube dampers by Bilstein (giving a bigger damper area).
- Spring aids by Bull for a more linear response.
- Lower wishbone strengthening spacer, tube and washer by ATP Northampton.
- Those lovely “Twist of pepper” wheels in “Liquid Boron” from Rimstock of Birmingham.
All of the above have been exhaustively and imaginatively tested by our Chassis team. Any failures in testing were addressed, components re-designed and the test re-started. Our end-of-test question is always “Would you rebuild that engine/gearbox/chassis, if it were your own car, i.e. your own safety that was dependent upon the state of the parts?” We don’t do “tick-box” engineering; we view it very seriously. The parts can pass the test and be a right mess, but that is not a pass; they have to have life after the test, unless it is deliberately destructive, such as a crash-test.
This is repeated until the design intent is met, tested and proved.
The same had to happen to the new decal set, which was the first time such an adventurous set of stripes was applied to a TF. This one feature alone has caused more debate and grief to those of us at Longbridge. We have conducted Honda “Gravelometer” tests to check for peeling of the stripes, we have done discolouration and weathering tests and poured all sorts of fluids on them. This was conducted for us by an independent test-house which is skilled in this activity.
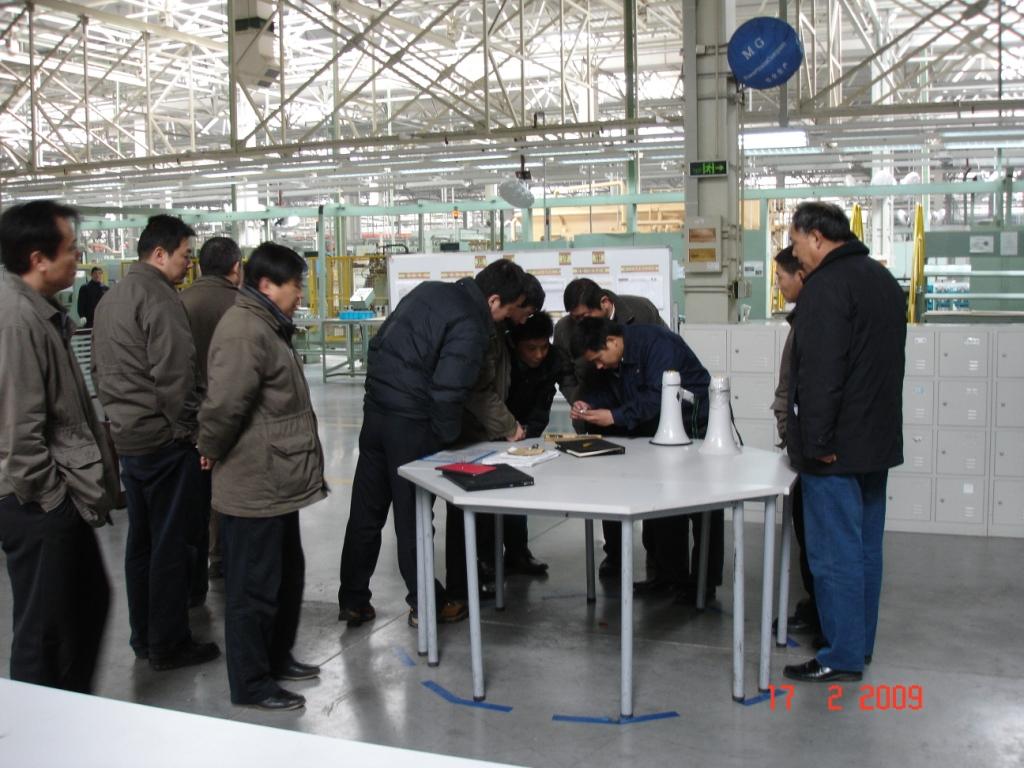
When this feature was approved, our search for a supplier ended up at GSM in Breconshire, who had given good service with the LE500 badges and are current supplier to the BMW MINI at Cowley. I was at pains to point out that the great BMW only manages to fit a very small number of cars with decals per day, with all their experience and wealth. The time to fit element has been quite emotive, as one must take time to create a quality job. There are fifteen parts to this decal set and each must be applied correctly. This is a real joint effort between Supplier, Engineer, Manufacturing and Quality.
The Board Director for SMPV (Shanghai Motor Passenger Vehicles) Mr Tao, has taken a keen, personal interest in this project and has given a specific, tight quality target for this aspect of the car. It was to him I had to address my request for passing the car over to Manufacturing to enter production in mid-July. Before he would give this, in early July I had held an ESO (Engineering Sign-off) event surrounded by all the new parts and the Engineers responsible. They presented parts and documentation to the Senior Management of MG Motor to gain acceptance that their job was completed. This was given with three small caveats (completed two weeks later).
It was excellent to have a man of Tao Hailong’s ability and detailed knowledge to present to and debate issues. He had visited us earlier in the year and taken a keen interest in our work. He asks all the right questions!
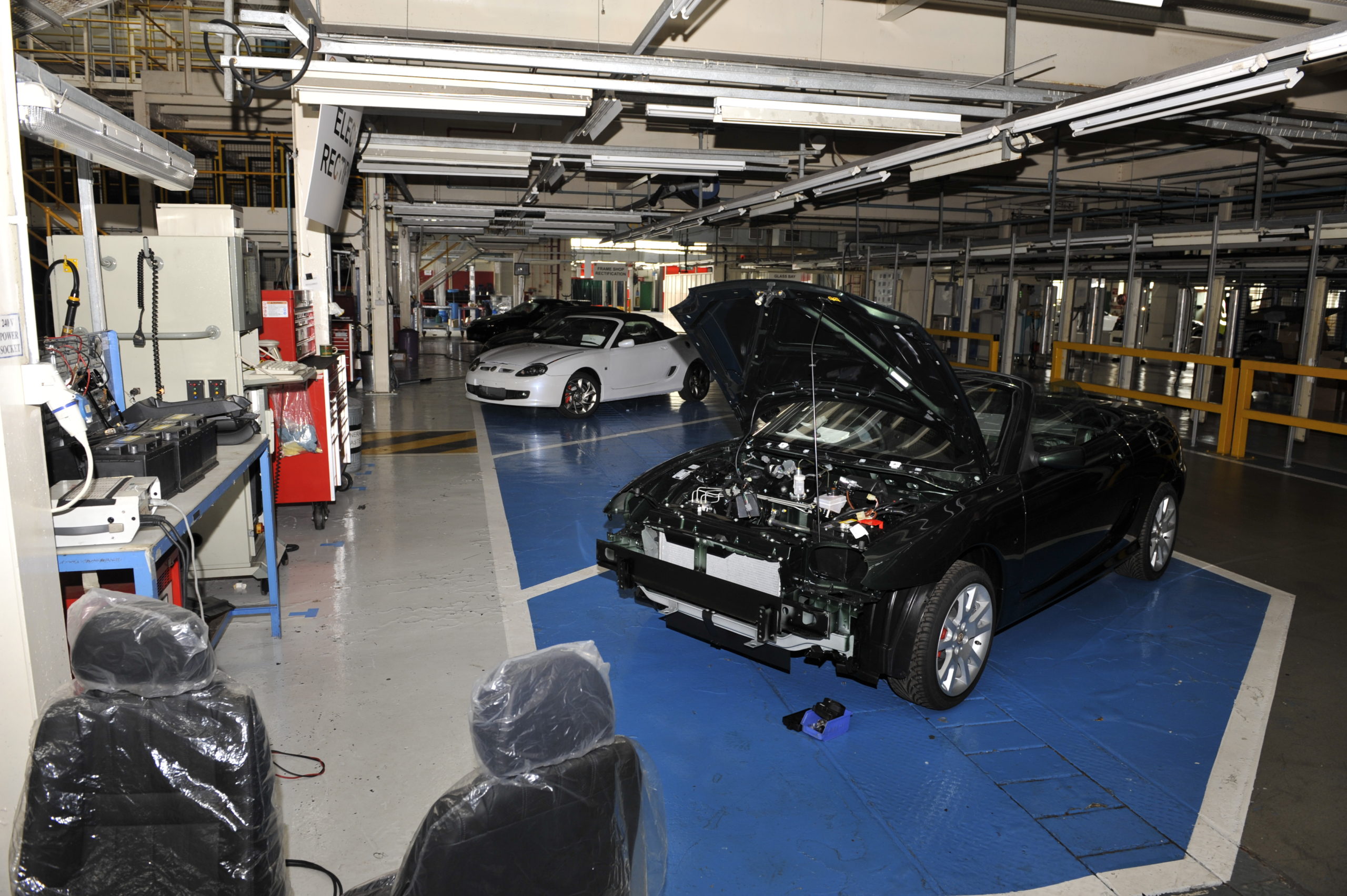
He also represents the many Engineers in China who are responsible for most of the MG TF Engineering these days. It has been interesting to work alongside those colleagues in China and to visit them from time to time. In February, I went to the MG Pukou engine plant in Nanjing, the old capital city, to assess the engine manufacturing facilities there, but that is for another time – it was very impressive, by the way.
So you see how the smallest washer, decal or any part must be thoroughly investigated.
Hence the time taken and the expense involved. Trained, experienced eyes and ears are necessary, qualified Engineers who can separate risk from reckless, pass from fail. Your safety is important to us; we like our customers to come back and tell us how much they enjoy our cars, and do you ever! Since taking on the TF work I have met many of you at events around the country and have taken some of you for a “Pogson Tour” of the factory in Longbridge. This is a great privilege and what comes back to me is how much you all love your MGs. I hope you trust us to fashion the next generation to your liking.
Ian Pogson CEng FIET
SMTC Longbridge
85th Anniversary Programme Manager
If you have enjoyed this article as much as I have writing it, there are more Pogson meanderings on life in China in my book, “Carry On Car-Making”, published by Brewin Books and available from the MG Car Club.